The Algorithmic Shift: Examination of AI's Impact on the Future of Manufacturing Work
- Tretyak
- Mar 22
- 7 min read
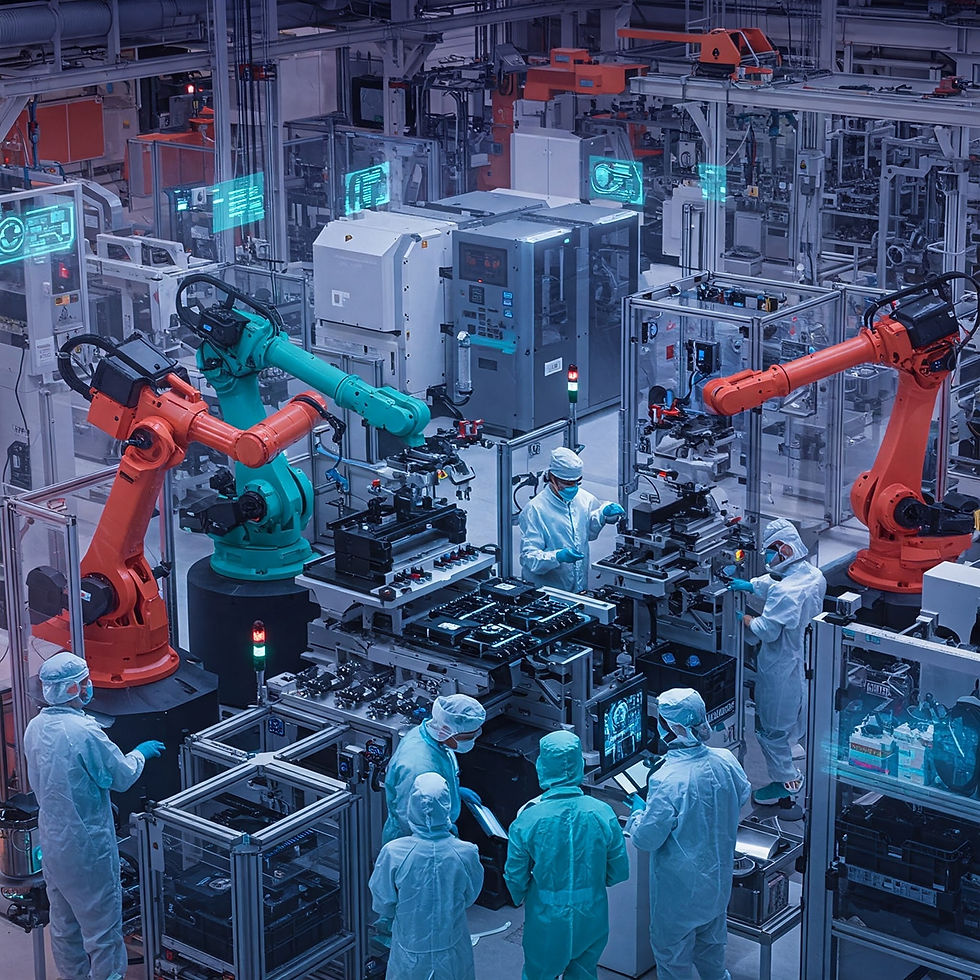
The manufacturing sector is undergoing a profound transformation, driven by the pervasive integration of Artificial Intelligence (AI). This isn't just a technological upgrade; it's an algorithmic shift, a paradigm change that will reshape the very nature of work, the roles of humans, and the skills required to thrive in the factories of tomorrow. Let's embark on a hyper-detailed exploration of AI's impact on the future of manufacturing work, dissecting the transformations, the challenges, and the opportunities that lie ahead.
How will AI impact the manufacturing workforce and job roles?
A Hyper-Transformation of Roles, Not Just Replacement, But a Cognitive Augmentation and New Skill Demands
AI will impact the manufacturing workforce and job roles in profound and multifaceted ways, extending far beyond simple automation and leading to a fundamental reconfiguration of the industrial landscape:
Automation of Repetitive and Dangerous Tasks: The Rise of Cognitive Automation:
AI-powered robots and automation systems will transcend basic automation, taking over not only routine, repetitive, and physically demanding tasks, but also cognitively demanding tasks that require precision, accuracy, and efficiency.
Example: Robots will handle intricate assembly tasks with adaptive dexterity, material handling with autonomous navigation, and quality control inspections with hyper-spectral vision, freeing up human workers from these tasks and minimizing workplace hazards.
Augmentation of Human Capabilities: The Era of Human-Machine Symbiosis:
AI will augment human capabilities, providing workers with sophisticated tools, real-time insights, and intelligent assistance to perform their jobs more effectively and safely.
Example: AI-powered augmented reality (AR) systems will provide workers with step-by-step instructions on complex assembly tasks, real-time guidance on equipment operation, and personalized safety alerts, enhancing their productivity and reducing errors.
Creation of New Roles: The Emergence of the AI-Driven Workforce:
AI will create new job roles in areas such as AI development, maintenance, oversight, and ethical governance, leading to the emergence of a specialized AI-driven workforce.
Example: AI engineers, data scientists, robot programmers, AI ethicists, AI trainers, and AI-assisted designers will be in high demand, requiring a new generation of skilled professionals.
Shift in Skill Requirements: The Cognitive and Adaptable Workforce:
The demand for manual labor will decrease, while the demand for cognitive, technical, and social-emotional skills will increase, requiring a fundamental shift in workforce training and education.
Example: Workers will need skills in data analysis, machine learning, AI programming, robotics, automation, problem-solving, critical thinking, creativity, and human-machine collaboration, as well as adaptability, communication, and emotional intelligence.
What training and upskilling programs are needed to prepare for AI-driven manufacturing?
Investing in Human Capital: A Hyper-Focused, Modular, and Continuous Learning Ecosystem
To prepare the workforce for the AI-driven future of manufacturing, a comprehensive and adaptive training and upskilling ecosystem is needed, encompassing various levels and modalities of learning:
Technical Skills Training: Building the Foundation of the AI Workforce:
Programs focused on data science, machine learning, AI programming, robotics, automation, and industrial IoT (IIoT) will be essential for equipping workers with the technical skills needed to design, develop, deploy, and maintain AI-powered manufacturing systems.
Example: Courses on Python programming for AI, TensorFlow and PyTorch frameworks, robotic control systems, sensor integration, and data analytics platforms will be crucial for developing a skilled AI workforce.
Digital Literacy Training: Empowering the Workforce in the Digital Age:
Programs that enhance digital literacy and the ability to use and interact with digital technologies effectively will be crucial for all workers in the AI-driven manufacturing environment.
Example: Training on data management, data analysis, digital collaboration tools, cybersecurity principles, and the use of AI-powered interfaces will be essential for empowering workers to navigate the digital landscape of the modern factory.
Problem-Solving and Critical Thinking Training: Cultivating Cognitive Agility:
Programs that develop problem-solving, critical thinking, and analytical skills will be essential for enabling workers to adapt to complex situations, troubleshoot issues, and make informed decisions in an AI-augmented environment.
Example: Workshops on design thinking, systems thinking, complex problem-solving methodologies, and decision-making frameworks will be crucial for developing a workforce that can effectively leverage AI to solve complex challenges.
Creative and Innovative Thinking Training: Fostering Human Ingenuity:
Programs that foster creativity, innovation, and adaptability will be crucial for enabling workers to generate new ideas, develop innovative solutions, and adapt to the ever-evolving landscape of AI-driven manufacturing.
Example: Training on design thinking, brainstorming techniques, creative problem-solving, and innovation methodologies will be essential for cultivating a workforce that can effectively collaborate with AI and contribute to the development of new products, processes, and business models.
Human-Machine Collaboration Training: Building Synergistic Partnerships:
Programs that focus on human-machine collaboration, communication, and teamwork will be essential for enabling workers to work effectively alongside AI-powered systems, robots, and other automated technologies.
Example: Training on how to work effectively with collaborative robots (cobots), interpret AI-generated insights, provide feedback to AI systems, and manage AI-driven workflows will be crucial for fostering a harmonious and productive partnership between humans and machines.
Ethical Training: Navigating the Moral Dimensions of AI:
Programs that educate workers on the ethical implications of AI in manufacturing will be crucial for ensuring responsible AI implementation and use.
Example: Training on responsible AI development, bias mitigation, data privacy, and ethical decision-making will be essential for cultivating a workforce that can navigate the moral complexities of AI and ensure that it is used for good.
How can industries address concerns about job displacement due to AI?
A Proactive, Multifaceted, and People-Centered Approach to Workforce Transition
Addressing concerns about job displacement due to AI requires a proactive, multifaceted, and people-centered approach, involving collaboration between industry, government, education, and individuals:
Invest in Workforce Retraining and Upskilling: Building a Future-Ready Workforce:
Provide opportunities for workers to learn new skills and transition to new roles, equipping them with the knowledge and abilities needed to thrive in an AI-driven economy.
Example: Company-sponsored training programs, partnerships with educational institutions, online learning platforms, and apprenticeship programs can provide workers with the skills and experience necessary for in-demand roles.
Promote Job Creation in Emerging Fields: Fostering Innovation and Opportunity:
Support the development of new industries and job roles that are created by AI, such as AI development, maintenance, oversight, and ethical governance.
Example: Incubators and accelerators for AI-related startups, government initiatives to promote AI innovation and entrepreneurship, and policies that encourage the creation of new businesses and industries that leverage AI technology.
Implement Social Safety Nets: Providing Support and Security:
Explore and implement social safety nets, such as unemployment benefits, universal basic income, and transition assistance programs, to support workers who may be displaced by AI.
Example: Expanding unemployment benefits to cover workers who lose their jobs due to automation, providing financial assistance for retraining and relocation, and exploring the feasibility of universal basic income to ensure a basic level of economic security for all citizens.
Foster Collaboration Between Industry, Government, and Education: Building a Collaborative Ecosystem:
Create partnerships between industry, government, and education to develop effective solutions for workforce transition, ensuring that education and training programs are aligned with industry needs and that workers have access to the resources and support they need to adapt to the changing landscape of work.
Example: Industry-led initiatives to define the skills needed for the AI-driven workforce, government funding for education and training programs, and educational institutions developing curricula that incorporate AI-related skills.
Focus on Human-AI Collaboration: Emphasizing the Synergistic Partnership:
Emphasize the potential for AI to augment human capabilities, rather than replace them, highlighting the benefits of human-AI collaboration and fostering a positive view of AI in the workplace.
Example: Promoting the development of collaborative robots (cobots) that work alongside human workers, enhancing their productivity and safety, and emphasizing the importance of human skills, such as creativity, critical thinking, and emotional intelligence, in an AI-driven environment.
Promote Transparency and Communication: Building Trust and Understanding:
Communicate openly and transparently about the impact of AI on the workforce, addressing concerns and fostering trust among employees, unions, and the public.
Example: Companies providing clear information about their AI implementation plans, the potential impact on jobs, and the support they are providing to workers who may be affected, as well as engaging in open dialogue with unions and community stakeholders to address concerns and build consensus.
How can manufacturers use AI to improve employee safety?
AI as a Guardian Angel: Enhancing Workplace Safety through Intelligent Automation
Manufacturers can leverage AI to improve employee safety in numerous ways, creating a safer and healthier work environment:
Predictive Safety Analytics:
Description: AI algorithms analyze sensor data from equipment, worker behavior, and environmental conditions to predict potential safety hazards and prevent accidents before they occur.
Example: AI analyzes data from wearable sensors to detect signs of worker fatigue or stress, predicting potential accidents and providing timely interventions.
Real-Time Hazard Detection and Warning Systems:
Description: AI-powered vision systems monitor the workplace to detect hazards, such as spills, obstructions, or unsafe worker behavior, and provide real-time warnings to prevent accidents.
Example: AI-powered cameras detect when a worker is entering a dangerous area and trigger an alert, preventing them from accessing hazardous zones.
Robotic Assistance and Ergonomic Optimization:
Description: Robots assist workers with physically demanding or repetitive tasks, reducing the risk of injuries and improving ergonomics.
Example: Collaborative robots (cobots) assist workers with heavy lifting or repetitive assembly tasks, reducing the risk of musculoskeletal disorders.
AI-Powered Safety Training and Simulation:
Description: AI creates immersive and interactive safety training simulations, allowing workers to practice safety procedures in a safe and controlled environment.
Example: Virtual reality (VR) simulations allow workers to practice emergency procedures or hazardous material handling techniques, providing a safe and realistic training experience.
Wearable Technology and AI-Driven Safety Monitoring:
Description: Wearable sensors monitor worker health and safety, providing real-time data on vital signs, movement, and environmental exposures, enabling proactive safety interventions and personalized health monitoring.
Example: Wearable sensors track worker heart rate, body temperature, and movement, detecting signs of heat stress or fatigue, and alerting supervisors to potential risks.
The algorithmic shift in manufacturing is not just about automation; it's about creating a safer, more productive, and more human-centered workplace. By embracing AI and prioritizing employee well-being, manufacturers can build a future where technology and humanity work together to create a thriving and secure industrial environment.
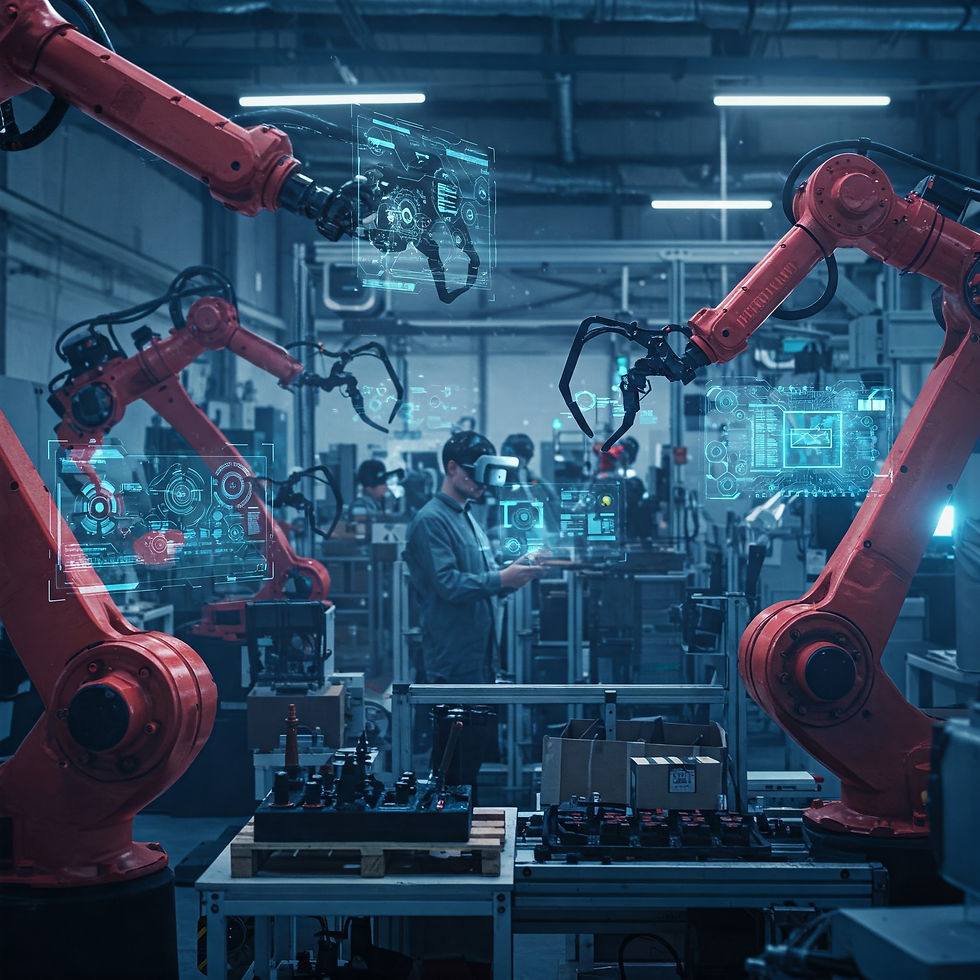
Comments